Troubleshooting
Oval Bores
Ensure the tool is the correct size for the bore to be honed. Thoroughly true in the stones, preferably to the exact bore diameter. If the part to be honed is thin walled, reduce the cutting pressure. If the stone stops cutting at reduced pressure, use a softer stone. For bores containing cut outs, large cross holes etc. use keyway type tooling.
Bellmouth Bores
Thoroughly true in the stones, preferably to the exact bore diameter. Reduce the stroke length and use tool with shorter stone length if available. If the bore length is less than 50% of the stone length reduce the stone length to 1½ times the bore length. If bell mouth persists continue to shorten stone or use a softer stone. Over correction will cause barreling.
Barrelled Bores
Thoroughly true in the stones, preferably to the exact bore diameter. Increase stroke length and use tool with longer stone length if available. If barreling persists shorten stone at both ends. Over correction will cause bell mouthing.
Combined Bellmouth / Barrel Bores
Typical in bores containing many cross holes, e.g. valve spool. Shorten stone length AND increase stroke length. If problem persists use softer stone.
Rainbow Bores (& Waviness)
Use long series tooling. Stone length should be at least 1 1/2 times the bore length. Correction of bent bores may result in bellmouthing. When bend has been corrected any bellmouthing can be corrected as described above.
Tapered Bores
Thoroughly true in the stones, preferably to the exact bore diameter. When honing manually reverse the component frequently. When honing automatically adjust stroke position to allow more stone to pass through the tight end of the bore.
Taper in Blind Bores
Thoroughly true in the stones, preferably to the exact bore diameter and reduce the stone length to 2/3 bore length. If the bore has insufficient or no relief at the blind end use short stone first to hone bottom of the bore. Use stone with hard tip. Ensure adequate supply of honing to blind bore.
Bent Bores
Use longest stone length available. Stone length should be at least 1½ times bore length. Correction of bent bores may result in bell mouthing. When bend has been corrected any bell mouth can be corrected as described above.
Stone Gazed
Stone does not cut
Open surface of stone with dressing stick
Increase stroking speed
Reduce rotation speed
Increase pressure
Use softer stone
Slow Stock Removal
If slow stock removal is not the result of stone glazed or loaded
Increase rotation speed
Increase pressure
Use softer stone
Use coarser stone
Pick Up
Reduce pressure
Reduce rotation speed
Use softer stone
Use finer stone
Change HS type mandrel to bronze or PT type
Ensure good flow of honing fluid
Check quality of honing fluid
Finish Too Fine
Open surface of stone with dressing stick
Increase stroking speed
Reduce rotation speed
Increase pressure
Use coarser stone
Use softer stone
Stone Loaded
Stone surface becomes clogged with material
Clean stone surface with dressing stick
Increase stroking speed
Use softer stone
Use coarser stone
Excessive Stone Wear
Reduce pressure
Increase rotation speed
Use harder stone
Use finer stone
Finish Too Rough
Thoroughly dress stone and shoe preferably to exact bore diameter
Increase rotation speed
Reduce pressure
Use finer stone
Check quality of honing fluid
Printable PDF
Superior Type Troubleshooting
A Common Honing Problem
What is overhooking?
Overhooking occurs when the bayonet of the mandrel wears and/ or the hook pin in the spindle that receives the bayonet wears. Overhooking of the mandrel throws torque onto the stone wires, which provides the chance for the stone wire to pull off the stone shoe at the weld joint, usually tearing a section of the stone wire, which is not designed to carry torque.
A check for this condition is easily made without inserting stone or turning on the machine. In the illustration below, the overhooking condition is show.
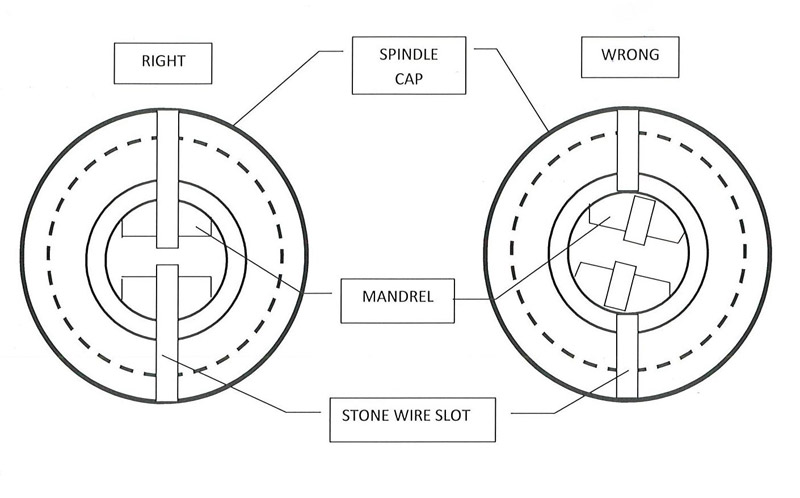
One more additional check – The hardened mandrel pilot bushing in the spindle will, in time, wear and need to be replaced. If these features are right, you will hone more easily and get the results you desire. If you have any questions please give Tennessee Abrasive a call.
Printable PDF
TROUBLESHOOTING CHART
WITNESSED CONDITIONS
ABRASIVE GLAZING
ABRASIVE LOADING
ABRASIVE GALLING
ABRASIVE SPALLING
FINISH TOO ROUGH
FINISH TOO SMOOTH
EXCESSIVE ABRASIVE USAGE
TAPERED STONE WEAR
ECCENTRIC STONE WEAR
SLOW STOCK REMOVAL
EXCESSIVE HEAT GENERATION
PART OUT OF ROUND
PART BELL MOUTHED TAPERED
PART NOT AXIALLY STRAIGHT
PART BEING HONED ECCENTRIC TO OD
SWIPE MARKS IN BORE
BORE NOT SQUARE TO FACE
WASHOUT AROUND KEYWAYS, PORTS
CORRECTIONS IN USUAL ORDER OF IMPORTANCE
2-3-5-15-13-18-11
2-3-15-7-17-19-11
2-3-7-15-0-17-19-24-11
30-6-22-23
1-4-6-17-16-7-12
2-3-5-18-15-8-13
1-4-6-16-7
12-22-21-16
14-22-21-16
5-3-2-8-11-15-18
10-6-8-11-24-15-20
6-2-3-12-14-15-25
26-12-14-25
31-14-25-32
14-28-29
27
28-14-32
6-17
CORRECTIONS
- INCREASE SPINDLE RPM
- DECREASE SPINDLE RPM
- INCREASE RECIPROCATION
- DECREASE RECIPROCATION
- INCREASE FEED RATE
- DECREASE FEED RATE
- INCREASE COOLANTS BASE CONTENT
- DECREASE COOLANTS BASE CONTENT
- CHECK FILTRATION OF COOLANT
- CHECK REFRIGERATION OF COOLANT
- CHECK COOLANT FOR HYDRAULIC OIL CONTAMINATION
- INCREASE RUN-OUT TIME
- DECREASE RUN-OUT TIME
- CHECK SPINDLE TO PART ALIGNMENT
- USE SOFTER ABRASIVES
- USE HARDER ABRASIVES
- USE FINER GRIT STONES
- USE COARSER GRIT STONES
- USE LESS POROUS STONES
- USE MORE POROUS STONES
- CHECK THAT ABRASIVES ARE ON GRADE
- CHECK TOOL SLOTS, PINS, CONE FOR WEAR
- TRIAL OTHER ABRASIVES
- USE MORE COOLANT
- CHECK TO SEE THAT FIXTURE IS NOT DISTORTING
- ADJUST OVER-RUN OF STROKE
- USE GUIDES
- TRAM PART FACE TO DETERMINE THAT PART IS SQUARE TO SPINDLE
- ROTATE PART OCCASIONALLY WHILE HONING
- USE LIGHT FEED PRESSURE AT START OF HONE
- USE LONGER ABRASIVES
- CHECK PART ACCURACY PRINT TO HONING
Printable PDF
HONING RELATIONSHIPS
RPM RECIPROCATION FEED RATE
INCREASING RPM
- Will make stones act harder
- Will give finer surface finishes
- Will cause a stone to stop cutting if increase is too great
- Will increase noise level
- Will decrease crosshatch angle
- Will decrease torque on part
- Will decrease geometric accuracies if increase is too great
DECREASING RPM
- Will make stone act softer
- Will give rougher surface finishes
- Will increase a stones’ ability to stay sharp and not glaze
- Will decrease noise level
- Will increase crosshatch angle
- Will increase torque on part
- Will allow bore to take greater possession of the tool, contributing to greater geometric accuracies
INCREASING RECIPROCATION SPEED
- Will make stones act softer
- Will give rougher surface finishes
- Will increase a stones’ ability to stay sharp and not glaze
- Will decrease noise level
- Will increase crosshatch angle
- Will remove stock slower if speed is too excessive
DECREASING RECIPROCATION SPEED
- Will make stones act harder
- Will give finer surface finishes
- Will decrease a stones’ ability to stay sharp and not glaze if too great
- Will increase noise level
- Will decrease crosshatch angle
- Will remove stock slower if speed is too slow
INCREASING FEED PRESSURE
- Will cause stones to act softer
- Will increase a stones’ ability to stay sharp and not glaze
- Will remove stock faster
- Will increase torque on the part
- Will contribute to geometric inaccuracies if too excessive
- Will increase wear on machine and tooling
- Will generate more heat
- Will generate more noise
- Will give rougher surface finishes
- Will wear abrasive if too excessive
Printable PDF
DECREASING FEED PRESSURE
- Will cause stones to act harder
- Will decrease stones’ ability to stay sharp and not glaze if reduced too much
- Will remove stock more slowly
- Will decrease torque on the part
- Will contribute to better geometric accuracies
- Will decrease wear on machine and tooling
- Will generate less heat
- Will generate less noise
- Will give finer surface finishes
- Will produce too long a time cycle stone light